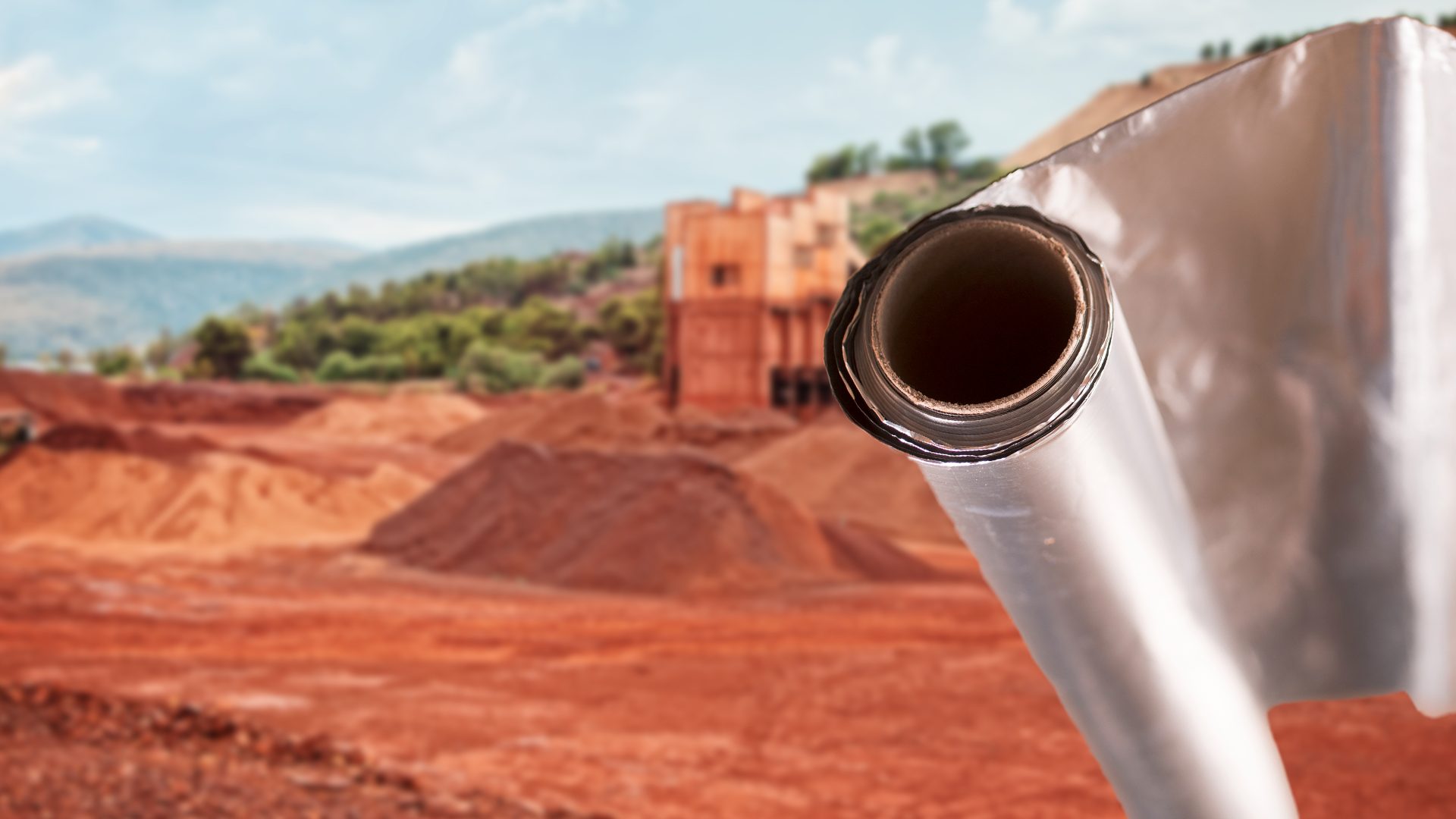
L'alluminio è un metallo di colore argento che non si trova in forma pura in natura: si trova in composti che costituiscono l'8% circa della crosta terrestre. Non viene quindi estratto, ma prodotto industrialmente attraverso il trattamento e la trasformazione della bauxite (una roccia sedimentaria ricca in minerali alluminosi, chiamata così perché fu scoperta a Lex Baux, in Provenza) oppure dalla rifusione di oggetti in alluminio, come le lattine. È sicuramente uno dei metalli più utilizzati nella nostra quotidianità: lo troviamo in molti oggetti di uso comune come lattine e altri imballaggi, fogli a rotolo (la cosiddetta "carta stagnola"), veicoli, finestre, porte, aerei, ferrovie e molto altro ancora. Solo in Italia, ogni anno vengono immesse sul mercato circa 81.000 tonnellate di imballaggi in alluminio e attualmente il Bel Paese è anche leader in Europa nel riciclo di questi prodotti, con oltre il 73% dell'alluminio utilizzato che viene poi riciclato.
La sua produzione può essere suddivisa in tre fasi principali: l'estrazione della bauxite, la produzione dell'allumina e la riduzione in alluminio.

Estrazione della bauxite
La bauxite è una roccia sedimentaria, di colore variabile dal rosso vivo al marrone, che può contenere fino a oltre 70% di minerali di idrossido di alluminio – come gibbsite, boehmite e diasporo – e viene estratta principalmente attraverso miniere a cielo aperto. Nel 2023, oltre 393 milioni di tonnellate di questo materiale sono state prodotte nel mondo, con oltre il 70% proveniente da Australia, Cina e Guinea. Seguono il Brasile, l'India e l'Indonesia nella classifica dei maggiori produttori.
Una volta estratta, la bauxite viene trasportata alle raffinerie, dove l'argilla e altre impurità superficiali vengono lavate. Il materiale pulito passa quindi attraverso un frantumatore per ridurre e uniformare le dimensioni dei frammenti e il passo successivo sarà quello dell’estrazione di allumina.
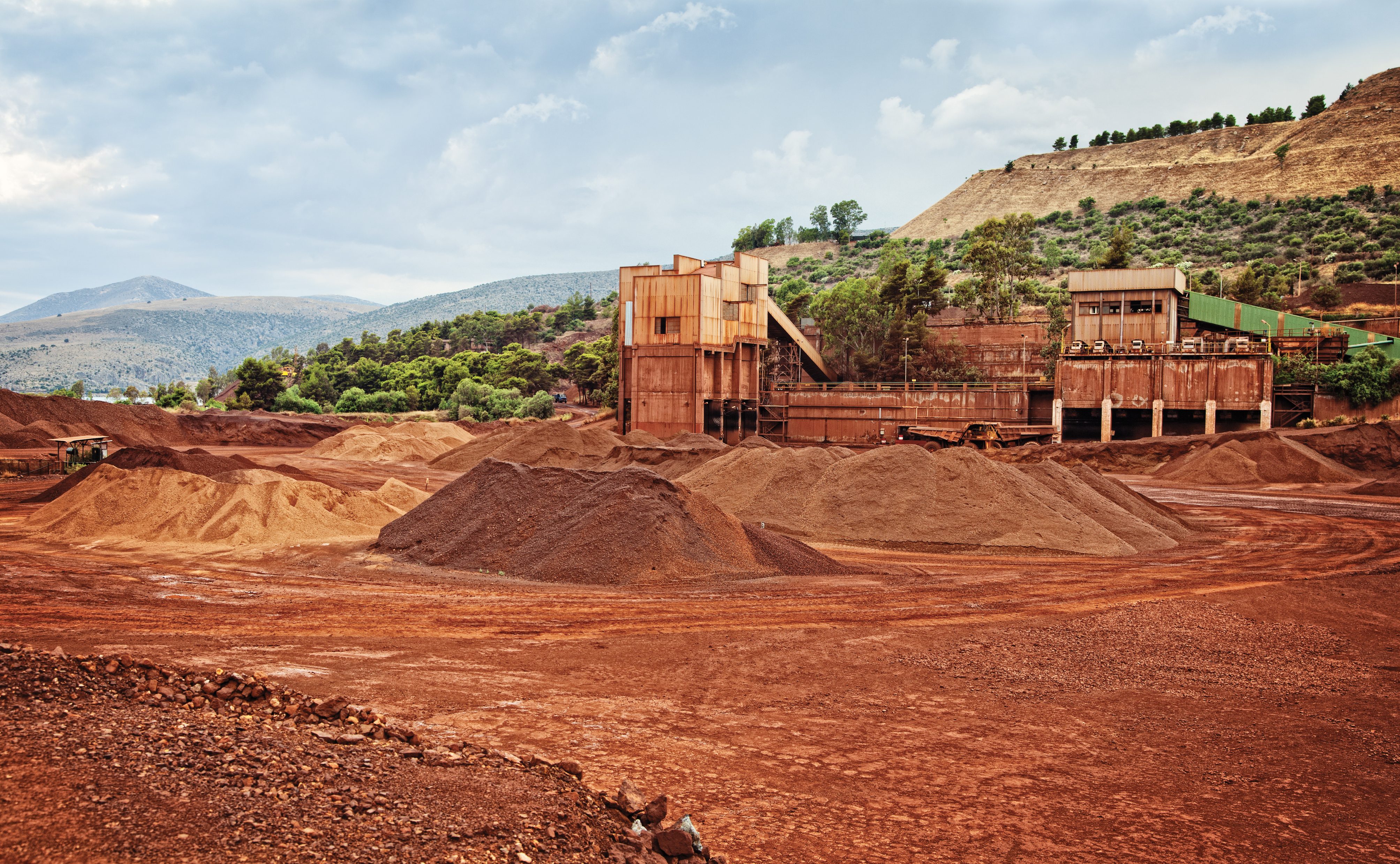
Produzione dell’allumina
L'allumina, o ossido di alluminio (Al2O3), è una polvere cristallina bianca o quasi incolore. In media, per produrre una tonnellata di ossido di alluminio sono necessarie circa 2.3 tonnellate di bauxite. Il processo di estrazione è stato sviluppato nel 1887 dal chimico austro-ungarico Carl Josef Bayer e si articola in quattro fasi successive: digestione, decantazione, precipitazione e calcinazione.
Digestione
Durante questa fase, la bauxite frantumata viene trattata con soda caustica (NaOH) e riscaldata a temperature che possono raggiungere i 270°C. In queste condizioni, la maggior parte dei minerali idrati di alluminio si sciolgono nella soda caustica, formando una soluzione di alluminato di sodio (NaAl(OH)4).
Decantazione
Il silicio, gli ossidi di ferro e titanio, i composti insolubili e le altre impurità presenti nella bauxite costituiscono il sottoprodotto del processo di digestione, noto come fango rosso. Si tratta una pasta marrone-rossastra, più densa, che si separa naturalmente dall'alluminato di sodio liquido depositandosi sul fondo delle cisterne di decantazione. Da qui, il fango rosso viene filtrato, lavato e poi smaltito in apposite aree di discarica.

Precipitazione
L’alluminato di sodio viene filtrato e trasferito in grandi cisterne, alcune delle quali possono essere alte quanto un palazzo di sei piani, e raffreddato. In queste nuove condizioni, si verifica la precipitazione dei cristalli di idrossido di alluminio (Al(OH)3) dalla soluzione. Per facilitare questo processo, vengono aggiunti nuclei o semi, che sono fondamentalmente piccoli cristalli di idrossido di alluminio, intorno ai quali si formeranno cristalli più grandi e puri. I cristalli prodotti nella fase di precipitazione vengono quindi filtrati e lavati con acqua, mentre la soluzione residua di soda caustica viene riscaldata nuovamente e re-immessa nel processo di produzione dell'allumina.
Calcinazione
Nella fase finale, gli idrossidi di alluminio vengono riscaldati a temperature fino a 1100°C all'interno di fornaci, chiamate calcinatori. Le alte temperature causano la rottura dei legami con le molecole di idrogeno e la trasformazione degli idrossidi di alluminio (Al(OH)3) in allumina (Al2O3).

Riduzione in alluminio
La trasformazione dell'allumina in alluminio avviene tramite un processo di riduzione elettrolitica chiamato processo Hall-Héroult. Questo processo implica la rimozione dell'ossigeno utilizzando una soluzione elettrolitica e il passaggio di corrente elettrica. La riduzione avviene all’interno di centinaia di vasche in acciaio rivestite da materiale refrattario, denominate celle elettrolitiche, collegate in serie. Questo processo richiede un'enorme quantità di energia elettrica, mediamente pari a 14.28 kWh per tonnellata di alluminio prodotta.
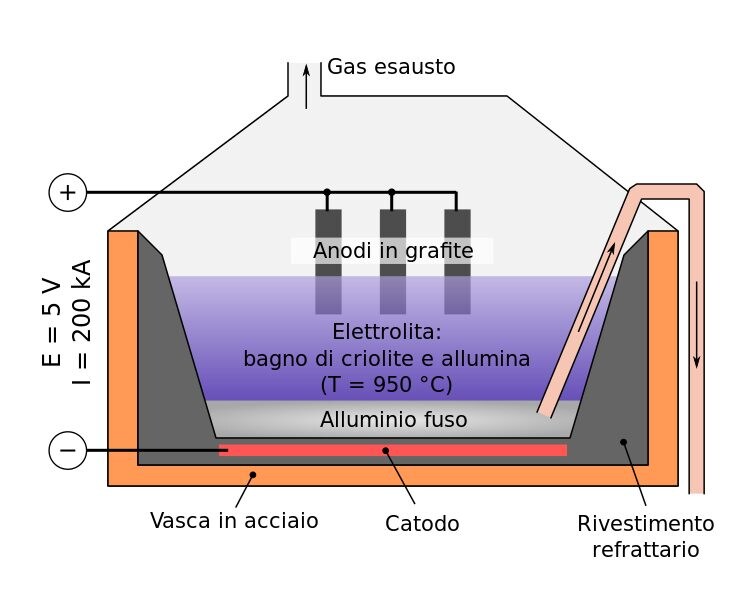
L'alluminio prodotto si accumula sul fondo della cella, da cui verrà estratto tramite un sifone. L’ossigeno, invece, reagisce con il carbonio degli elettrodi producendo anidride carbonica gassosa che viene gestita attraverso appositi sistemi di trattamento. In media, per ogni tonnellata di alluminio prodotta, vengono emessi circa 280.000 metri cubi di gas.
Trattamento finale e colatura
L'alluminio fuso viene trasportato in una fonderia dove viene raffinato in forni a temperature di circa 800 °C per eliminare le ultime impurità. Per aumentare la purezza del prodotto finale, l'alluminio può essere trattato con cloro o rame. Una volta pronto, il materiale viene versato negli stampi selezionati e lasciato solidificare.